Arc welding, applications of arc welding, equipments required in arc welding, advantages and disadvantages of arc welding, Gas Metal Arc Welding (GMAW/MIG), Gas Tungsten Arc Welding (GTAW/TIG), Shielded Metal Arc Welding (SMAW), Flux Cored Arc Welding (FCAW) – Arc welding – Basics, Equipments required, Advantages and Disadvantages.
Table of Contents
Arc Welding
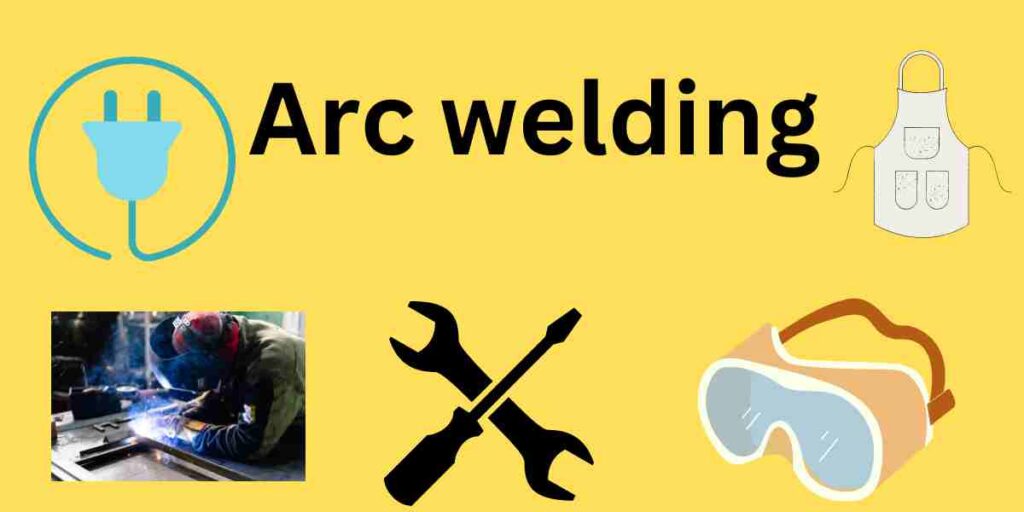
Arc welding is dependent on?
Any welding is basically dependent on generation of heat to melt welding part and using it to join two different metal parts. Similarly, in arc welding as well same thing happens.
Arc welding is a fusion welding process used to join metals.
(Fusion welding is the process that uses heat to join two materials by heating them to their melting point.)
In arc welding electric supply which can be AC or DC is provided between electrodes i.e. cathode and anode, which leads to generation of negatively charged electrons from cathode and moving at very high speed towards anode.
During this whole process kinetic energy of electrons is converted into heat energy.
Application of arc welding:
- In Vessels, pressurised vessels, pipes, tanks, ships etc.
Equipments required in arc welding are:
- Power supply which as we have already mentioned can be AC or DC,
- Electrodes can be bare or coated, in both of these the bare electrodes has somewhat less efficiency,
- Cables and connectors for providing electric supply at desires place,
- Earthing clamps to avoid any accident that can happen because of overflowing electricity,
- Wire brush for cleaning purpose after welding,
- Shield and protective gear like coat, black glass screen, shoes etc. to save oneself from heat, sparks etc.
Advantages and disadvantages of arc welding:
Advantages of Arc Welding:
- Better speed,
- Less post welding cleaning is required,
- Good weld quality,
- Less effort is required,
- Low hydrogen is required in arc welding etc.
Disadvantages of Arc Welding:
- High setup and upkeep cost in the starting,
- Setting up requires adequate technical know how,
- Radiation exposures are comparatively more harmful etc.
What are the different types of Arc Welding?
- Gas Metal Arc Welding (GMAW/MIG),
- Gas Tungsten Arc Welding (GTAW/TIG),
- Shielded Metal Arc Welding (SMAW), and
- Flux Cored Arc Welding (FCAW),
Each type has it’s own pros and cons.
Pros | Cons | |
Gas Metal Arc Welding (GMAW/MIG) | – Easy to learn, – Minimum cleanup required, – High welding speeds etc. | – Cost of shielding gas, – Inability o weld thicker metals etc. |
Gas Tungsten Arc Welding (GTAW/TIG) | – Produced most high-quality extremely strong welds, | – Difficult welding method as it requires high precision and skill, |
Shielded Metal Arc Welding (SMAW) | – Does not require shielding gas, – Works well on dirt and rusty materials, | – Welds are not very high quality as they are prone to porosity, cracks etc. |
Flux Cored Arc Welding (FCAW) | – Inexpensive and easy to learn, – High welding speed and portability, | – – |
Other relevant links:
- Earthing क्या होती है और इसके इस्तेमाल?
- ट्यूब-लाइट (Tube-light) कैसे काम करती है ? – semquestions
- What is noise in data mining MCQ?
- Arc welding – Wikipedia
Conclusion
We tried to give a brief overview about arc welding, components required for it, advantages and it’s disadvantages. Please let us know if you want us to cover anything else on this or any other topic.
FAQs
Q1. Do arc welding require safety equipments?
Yes, it’s very important to use safety equipment while doing arc welding.